Calculating the engineering cost of Fan Coil Units (FCUs) involves multiple components, including equipment cost, installation fees, material costs, and additional expenses. Below is a structured breakdown of how to estimate the total cost for an FCU system.
1. Determine System Scale
- Assess the project requirements and building layout to determine the quantity and type of FCUs needed.
- Different FCU models have varying capacities, efficiency ratings, and features, which impact overall cost.
2. Equipment Cost Calculation
- Multiply the unit price of each FCU by the total quantity required.
- Consider different models based on:
- Cooling/heating capacity
- Energy efficiency ratings
- Brand reputation and durability
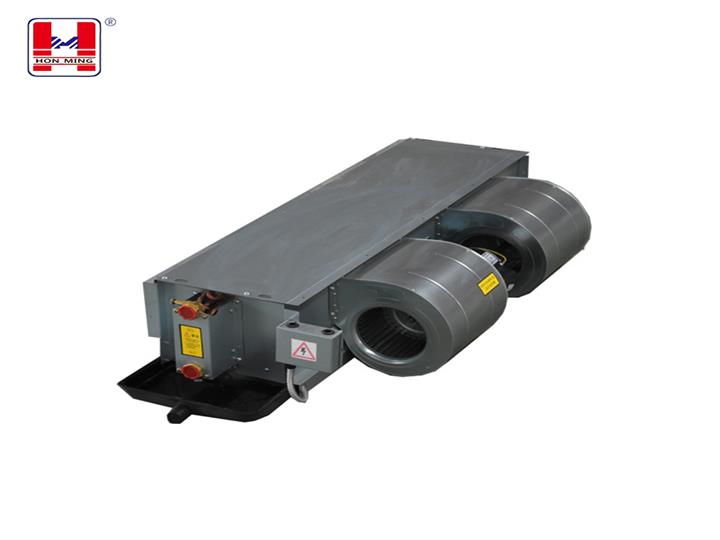
3. Installation Fees
- Labor costs depend on installation complexity:
- Simple installations (e.g., surface-mounted units) have lower labor costs.
- Ceiling-recessed or wall-embedded installations may require higher labor expenses.
- If the installation is at height (e.g., in high-rise buildings), a height coefficient adjustment may apply to increase labor rates.
4. Material Costs
- Piping and insulation:
- Copper pipes, PVC pipes, or PPR pipes for water connections.
- Insulation material to minimize heat loss and condensation.
- Electrical wiring and accessories:
- Wiring for power and control systems.
- Conduits and junction boxes for electrical safety.
- Mounting brackets and supports:
- Wall or ceiling mounting structures.
- Ductwork (if applicable):
- Some FCU systems require additional air ducts, increasing material costs.
5. Auxiliary Equipment and Accessories
- Valves: Two-way or three-way valves for water flow control.
- Thermostats: Wired or wireless control units for temperature regulation.
- Filters: Additional air filtration components.
6. Design and Commissioning Costs
- Engineering design fees:
- HVAC engineers may charge for layout planning and system integration.
- System testing and commissioning:
- Ensuring the FCU system operates efficiently and meets performance standards.
7. Additional Expenses
- Scaffolding costs (if installation is at height).
- Project management and supervision fees.
- Taxes and administrative fees.
8. Detailed Bill of Quantities (BOQ)
- A structured engineering quantity list includes:
- Number of FCUs.
- Length of piping and cabling required.
- Specific accessories and additional installation details.
9. Adjustment Factors and Cost Coefficients
- Based on local construction regulations or industry standards, adjustment coefficients may be applied:
- Difficult installation conditions (e.g., confined spaces, high altitudes) → Cost multiplier 1.2–1.5.
- Urgent project timelines → Labor cost increase 10–20%.
10. Budget and Quotation Preparation
- Sum up all equipment, installation, materials, and additional costs to prepare a final budget.
- Consult with HVAC suppliers, contractors, and cost estimators to refine pricing.
Conclusion
Calculating the cost of an FCU system requires a detailed evaluation of equipment, materials, labor, and project-specific conditions. For precise cost estimates, it’s advisable to work with HVAC professionals, suppliers, and construction cost consultants to align with market conditions and project requirements.